CARACTERÍSTICAS FÍSICAS QUÍMICAS DE LAS FIBRAS SINTÉTICAS
- paulinaosoriovalen
- 26 jun 2015
- 38 Min. de lectura
POLIESTER
Las fibras de poliéster son 50% cristalinas y el Angulo de sus moléculas puede variar. Sus propiedades son muy sensibles a los procesos termodinámicos. Básicamente el poliéster, a través de modificaciones químicas y físicas, puede ser adaptado hacia el uso final que se le va a dar, como puede ser fibras para ropa, textiles, para el hogar o simplemente filamentos o hilos
Una característica importante del poliéster es su alta elasticidad, que hace que este sea más conveniente para artículos que no cambien mucho de forma como ropa interior o para ropa exterior ya que tienen que mostrar alta estabilidad y forma consistente
Las principales propiedades del poliéster son (carty, 1996):
· Bajo amplificación, la fibra parece lisa y en forma de barra. Usualmente es circular en zonas transversales.
· Es usado como un filamento continuo ( usualmente texturizado)
· Normalmente tiene mucho brillo, pero es meno vidrioso en apariencia que el nylon
· Son extremadamente fuertes y resistentes a la abrasión.
· Es extensible y no se arruga fácilmente. Es resistente al estiramiento
· Conserva mejor el calor que el algodón y el lino
· No es absorbente
· Es resistente a los ácidos, álcalis y blanqueadores.
· El poliéster e termoplástico. Con ayuda del calor, se pueden producir plisados y pliegues permanentes.
· Alta resilencia
· Alta resistencia a la tracción y a la humedad
· Son estables ante los rayos ultra violetas
· Buena resistencia eléctrica
· Son biodegradables
Desventaja
Fuerte carga electrostática
Propiedades bajas de absorción de agua
Tendencia al peeling
Fabricación de vestidos, blusas, trajes, ropa, impermeables, ropa deportiva, ropa interior y lencería.
· Fabricación de envases para bebidas
· Fabricación de vasijas en la ingeniería, medicina, agricultura etc.
· Sutura o fijación ósea o para sustituir fragmentos óseos (biomedicina)
· Fabricación de juguetes, agentes adhesivos, colorantes y pinturas
· Fabricación de componentes eléctricos y electrónicos
· Fabricación de cintas adhesivas, hilos de refuerzo para neumáticos.
· Fabricación de carcasas, interruptores, capacitores.
· Piezas para la industria automotriz
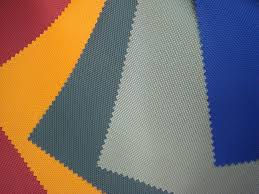
POLIAMIDA
Características del polipropileno y la poliamida.
Polipropileno:
Polipropileno (PP) es un polímero termoplástico, parcialmente cristalino, pertenece al grupo de las poliolefinas y utilizado en una amplia variedad de aplicaciones que incluyen textiles. Este polímero se obtiene de la polimerización del propileno (o Propeno) que es su monómero y tiene gran resistencia contra diversos solventes químicos, así como contra alcalis y ácidos.
Propiedades físicas y químicas del Polipropileno:
El polipropileno comercial estándar tiene un grado de cristalinidad intermedio entre el polietileno de alta y el de baja densidad; su módulo elástico también es intermedio, es menos duro que el PEAD y menos quebradizo.
Polipropileno presenta muy buena resistencia a la fatiga. Las propiedades dieléctricas del polipropileno son utilizadas en películas muy delgadas formando capacitores con un buen desempeño.
El polipropileno y el polietileno son dos de los termoplásticos más utilizados. Se pueden encontrar en natural o aditivados con fibra de vidrio/carga mineral. Para darle más resistencia y/o rigidez, y estabilidad dimensional.
Son materiales que soportan bien los agentes químicos. También los podemos encontrar resistente UV y/o ignífugos. Son utilizados de forma amplia en todas las áreas de actividad, incluidos los textiles…
Características
Rango de temperatura de trabajo 0ºC +100ºC.
Posee una gran capacidad de recuperación elástica.
Resiste al agua hirviente, pudiendo esterilizarse a temperaturas de 140ºC sin deformación.
Resiste a las aplicaciones de carga en un ambiente a una temperatura de 70ºC sin producir deformación.
Gran resistencia a la penetración de los microorganismos.
Gran resistencia a los detergentes comerciales a una temperatura de 80ºC.Debido a su densidad flota en el agua.
Una poliamida es un tipo de polímero que contiene enlaces de tipo amida. Las poliamidas se pueden encontrar en la naturaleza, como la lana o la seda, y también ser sintéticas, como el nailon o el Kevlar.
Las poliamidas como el nailon se comenzaron a emplear como fibras sintéticas, aunque han terminado por emplearse en la fabricación de cualquier material plástico.
Las aramidas son un tipo de poliamidas en las que hay grupos aromáticos formando parte de su estructura. Por ejemplo, se obtienen fibras muy resistentes a la tracción o fibras también muy resistentes al fuego.
Las poliamidas se pueden aditivar con fibra de vidrio, molibdeno, grafito, teflón... con ello conseguimos aumentar la resistencia a la fricción , al calor, aumentar el impacto, estabilidad dimensional… También los podemos encontrar ignífugas.
Las poliamidas son materiales versátiles que se utilizan en numerosas aplicaciones; automoción, equipos industriales, maquinaria, engranajes, soportes, y en general en piezas que sufran mecánicamente.
Características
Rango de temperatura de trabajo -40ºC +90ºC.
Alta resistencia mecánica.
Buena resistencia a la fatiga.
Alto poder amortiguador.
Buenas propiedades de deslizamiento.
Resistencia sobresaliente al desgaste.
Autoextingible.

TEFLON
Politetrafluoroetileno
Fórmula del monómero de Teflón.
El Teflón (PTFE) es un polímero similar al polietileno, en el que los átomos de hidrógeno han sido sustituidos por átomos flúor. La fórmula química del monómero, tetrafluoroeteno, es CF2=CF2. .
Bajo el nombre de Teflon, también llamado Teflón en algunas regiones, la multinacional DuPont comercializa este y otros cuatro polímeros de semejante estructura molecular y propiedades. Entre ellos están la resina PFA (perfluoroalcóxido) y el copolímero FEP (Propileno Etileno Flurionado), llamados Teflon-PFA y Teflon-FEP respectivamente. En la siguiente figura se muestra la fórmula del PFA (perfluoroalcóxido):
Tanto el PFA como el FEP comparten las propiedades características del PTFE, ofreciendo una mayor facilidad de manipulación en su aplicación industrial.
PROPIEDADES
La virtud principal de este material es que es prácticamente inerte, no reacciona con otras sustancias químicas excepto en situaciones muy especiales. Esto se debe básicamente a la protección de los átomos de flúor sobre la cadena carbonada. Esta carencia de reactividad hace que su toxicidad sea prácticamente nula; además, tiene un muy bajo coeficiente de rozamiento. Otra cualidad característica es su impermeabilidad, manteniendo además sus cualidades en ambientes húmedos.
No obstante, un subproducto presente en el teflón, el ácido perfluorooctanoico, resulta, además de contaminante (no es biodegradable), potencialmente cancerígeno para el ser humano. Incluso, ha sido relacionado con la infertilidad, los trastornos inmunitarios y problemas de crecimiento prenatal.
Es también un gran aislante eléctrico y sumamente flexible, no se altera por la acción de la luz y es capaz de soportar temperaturas desde -270°C(3,15 K) hasta 270 °C (543,15 K), momento en que puede empezar a agrietarse y producir vapores tóxicos. Su cualidad más conocida es la antiadherencia.
En revestimientos de aviones, cohetes y naves espaciales debido a las grandes diferencias de temperatura que es capaz de soportar.
En la industria se emplea en elementos articulados, ya que su capacidad antifricción permite eliminar el uso de lubricantes como el Krytox.
En medicina, aprovechando que no reacciona con sustancias o tejidos y es flexible y antiadherente se utiliza para prótesis, creación de tejidos artificiales y vasos sanguíneos, en incluso operaciones estéticas (body piercing).
En electrónica, como revestimiento de cables o dieléctrico de condensadores por su gran capacidad aislante y resistencia a la temperatura. Los condensadores con dieléctrico de teflón se utilizan en equipos amplificadores de sonido de alta calidad. Son los que producen menores distorsiones de audiofrecuencias. Un poco menos eficientes, les siguen los de poliester metalizado (MKP).
En utensilios de cocina, como sartenes y ollas por su capacidad de rozamiento baja, así son fáciles de limpiar y mantiene un grado menor de toxicidad.
En pinturas y barnices.
En estructuras y elementos sometidos a ambientes corrosivos, así como en mangueras y conductos por los que circulan productos químicos.
Como recubrimiento de balas perforantes. El teflón no tiene efecto en la capacidad de perforación del proyectil, sino que reduce el rozamiento con el interior del arma para disminuir su desgaste.
Como hilo para coser productos expuestos continuamente a los agentes atmosféricos.
En Odontología como aislante, separador y mantenedor del espacio interproximal durante procedimientos de estética o reconstrucciones con resinas compuestas o composite.

KEVLAR
El Kevlar o poliparafenileno tereftalamida es un polímero altamente cristalino. Llevó mucho tiempo encontrar alguna aplicación útil para el Kevlar, dado que no era soluble en ningún disolvente. Por lo tanto, su procesado en solución estaba descartado. No se derretía por debajo de los 500ºC, de modo que también se descartaba el hecho de procesarlo en su estado fundido.
Stephanie Kwolek trabajaba en un laboratorio para DuPont, donde todos los días experimentaba con nuevos materiales. Descubrió el Kevlar cuando se dio cuenta de que una solución plástica que ella estudiaba a menudo estaba actuando de manera "diferente". La obtención de las fibras de Kevlar fue complicada, destacando el aporte de Herbert Blades, que solucionó el problema de qué disolvente emplear para el procesado. Este material era súper resistente y a la vez muy ligero. Así fue como descubrió el Kevlar, una fibra química famosa por su uso en los chalecos antibalas.
Nomex:
Las características intrínsecamente ignífugas proporcionadas por NOMEX® hacen que las personas que trabajan con este polímero estén seguras y protegidas contra los peligros del trabajo de cada día. Es ese conocimiento y sentido de la seguridad el que les permite concentrarse en su tarea actual, y contribuir así a elevar la productividad.
NOMEX® esuna molécula con cadena larga. La tecnología térmica avanzada fue creada hace más de 30 años cuando los científicos de DuPont crearon una fibra con una combinación extraordinaria en cuanto a características de alto rendimiento `para el calor e ignífugas, así como características superiores del textil.
La familia de DuPont de los productos de fibra de NOMEX® proporciona resistencia excepcional al calor y a la llama y ofrece características excelentes del textil. Los usos incluyen los filtros, las telas revestidas industriales, etc.
NOMEX® también se utiliza para el aislamiento eléctrico en forma de papel y de cartón prensado, donde su fuerza dieléctrica inherente, dureza mecánica y estabilidad termal proporcionan alta confiabilidad en los usos más exigentes.
Estructura química del Kevlar y del Nomex:
Pertenecen a la familia de las aramidas, las cuales, a su vez, pertenecen a una familia de nylons.
Una sola cadena del polímero de Kevlar podría tener desde cinco hasta un millón de monómeros enlazados juntos. Cada monómero de Kevlar es una unidad química que contiene 14 átomos de carbono, 2 átomos de nitrógeno, 2 átomos de oxígeno y 10 átomos de hidrógeno.
El Kevlar es una poliamida, en la cual todos los grupos amida están separados por grupospara-fenileno, es decir, los grupos amida se unen al anillo fenilo en posiciones opuestas entre sí, en los carbonos 1 y 4.
El Nomex, por otra parte, posee grupos meta-fenileno, es decir, los grupos amida se unen al anillo fenilo en las posiciones 1 y 3.
Las aramidas se utilizan en forma de fibras. Forman fibras aún mejores que las poliamidas no aromáticas, como el nylon 6,6.
Las cadenas del polímero se pueden juntar aleatoriamente o se pueden orientar cuidadosamente de lado a lado en una fila. Resulta que la orientación de las cadenas del polímero es muy importante para ciertas características tales como flexibilidad, rigidez, y fuerza.
Una fibra de Kevlar es un arsenal de moléculas orientadas en paralelo como un paquete de espaguetis crudos. Esta colocación espacial es lo que proporciona las moléculas con estructura cristalina. La cristalinidad es obtenida por un proceso de fabricación que implica sacar la solución fundida del polímero a través de agujeros pequeños de la extrusora. La cristalinidad de los filamentos del polímero de Kevlar contribuye perceptiblemente a su fuerza y rigidez únicas.
Las amidas tienen la capacidad de adoptar dos formas diferentes, o conformaciones. Usted puede ver ésto en la figura de una amida de bajo peso molecular. Las dos figuras son del mismo compuesto, en dos conformaciones diferentes. La que está a la izquierda se denomina conformación trans, y la que está a la derecha conformación cis.
En latín, trans significa "del otro lado". Así, cuando las cadenas hidrocarbonadas de la amida están en lados opuestos al enlace peptídico, el enlace entre el oxígeno del carbonilo y el nitrógeno de la amida, ésta se denomina amida trans. Asimismo, cis en latín significa "en el mismo lado", y cuando las cadenas hidrocarbonadas están del mismo lado del enlace peptídico, la llamamos amida cis.
La misma molécula de la amida puede torcerse hacia adelante y hacia atrás entre las conformaciones cis y trans, originando una pequeña energía.
En las poliamidas también existen las conformaciones cis y trans. Cuando en una poliamida todos los grupos amida están en su conformación trans, como el nylon 6.6 por ejemplo, el polímero se estira completamente en una línea recta.
Esto es exactamente lo que deseamos para las fibras, porque las cadenas largas y completamente extendidas se empaquetan más adecuadamente, dando lugar a la forma cristalina que caracteriza a las fibras. Pero lamentablemente, siempre existen unos pocos enlaces amida en la conformación cis. Por ello las cadenas del nylon 6.6 nunca llegan a estar completamente extendidas.
Sin embargo el Kevlar es diferente. Cuando intenta adoptar la conformación cis, los hidrógenos de los voluminosos grupos aromáticos se interponen en el camino. La conformación cis coloca a los hidrógenos un poco más cerca de lo que quisieran estar. De este modo, el Kevlar permanece casi enteramente en su conformación trans. Y así, puede extenderse completamente para formar unas hermosas fibrasUna fibra de Kevlar es en realidad un conjunto de cadenas de polímeros
La idea de la atracción entre imanes es una analogía que ayuda en entender las fuerzas atractivas entre las cadenas del polímero. Las cadenas individuales del polímero se unen realmente por fuerzas electrostáticas que hay entre las moléculas, conocidas como enlaces por puentes de hidrógeno, que se forman entre los grupos de amidas polares en cadenas adyacentes.
En cuanto a los enlaces por puentes de hidrógeno, el Kevlar y el agua tienen algo en común. En ambos compuestos, los átomos de oxígeno tienen una alta densidad de electrones alrededor del núcleo. Puesto que los electrones se cargan negativamente, los átomos de oxígeno tendrán una carga negativa leve. Por otra parte, los átomos de hidrógeno tienen una densidad mucho más baja de electrones alrededor del núcleo, teniendo, por tanto, una carga positiva parcial. El hidrógeno y el oxígeno de diversas moléculas se atraen, formando el enlace por puentes de hidrógeno.
Propiedades del Kevlar y del Nomex
Las propiedades de estos dos materiales van ligadas intrínsecamente a las aplicaciones que podemos encontrar tanto en la industria como en la vida cotidiana, las cuales se ven en el siguiente punto.
No derriten ni se contraen en llama, y carbonizan solamente a temperaturas muy altas. Ofrecen una resistencia excelente al agua y al petróleo, incluyendo el aceite de motores y lubricantes, además tienen una buena resistencia química y son químicamente estables bajo una gran variedad de condiciones de exposición. Son ambos extremadamente resistentes y con alta resistencia a la abrasión, además se cortan y se rasgan.
NOMEX® es un polímero aromático sintético de poliamida que proporciona altos niveles de la integridad eléctrica, química y mecánica.
Esto es lo que hace que NOMEX® no se contraiga, ni dilate, ni se ablande ni derrita durante la exposición a corto plazo a temperaturas tan altas como 300°C. A largo plazo puede estar trabajando como aislante tanto térmico como eléctrico o químico soportando continuamente temperaturas de hasta 220°C durante más de 10 años.
La fuerza y la resistencia de los papeles y de los cartones prensados de NOMEX® ayudan a ampliar vida del equipo que rota en condiciones de funcionamiento severas. Estas condiciones incluyen choque severo y vibraciones excesivas propiciadas por desequilibrios rotantes, como por ejemplo las que pueden aparecer en molinos de acero, motores para tracción ferroviaria, o turbinas de gas. En todos ellos además tenemos grandes temperaturas de funcionamiento.
Fuerza dieléctrica inherente
En tensiones eléctricas muy elevadas, como cortocircuitos, a corto plazo los productos de NOMEX® de 18 a 40 V/mil de kV/mm (457 a 1015), dependiendo de tipo de producto y grueso, proporcionan la protección necesaria y adecuada.
Dureza mecánica
Los productos de alta densidad de NOMEX® son fuertes, resistentes y (en los grados más finos) flexibles, con buena resistencia al rasgado y a la abrasión. Sometido a presión hidrostática, el Kevlar es 20 veces más fuerte que el acero.
Estabilidad termal
Las temperaturas hasta 200°C tienen poco o nada de efecto en las características eléctricas y mecánicas de los productos de NOMEX®, y los valores útiles se conservan en temperaturas considerablemente más altas. Además, estas características útiles se mantienen por por lo menos 10 años de exposición continua a 220°C de temperatura.
Compatibilidad química
NOMEX® es esencialmente inerte a la mayoría de los disolventes, y es totalmente resistente a los ataques de ácidos y álcalis. Es compatible con todas las clases de barnices y de pegamentos, de líquidos de transformadores, de aceites lubricantes, y de refrigerantes. Puesto que los productos de NOMEX® no son digestibles, no son atacados por insectos, hongos, etc.
Capacidades criogénicas
NOMEX® ha encontrado una gran aceptación en una variedad de usos criogénicos debido a su estructura polimérica única. En el punto que hierve el nitrógeno (77°K), los cartones prensados de papel de NOMEX® resisten plenamete las fuerzas de contracción/dilatación que aparecen.
Insensibilidad a la humedad
En equilibrio con un 95 por ciento de humedad relativa, los papeles de NOMEX® y los cartones prensados mantienen un 90 por ciento de su fuerza dieléctrica, mientras que muchas características mecánicas además mejoran.
Resistencia de la radiación
NOMEX® es esencialmente inafectado por 800 megarads (8Mgy) de radiación de ionización y todavía conserva características mecánicas y eléctricas útiles después de ocho veces esta exposición.
No toxicidad
Los productos de NOMEX® no producen ninguna reacción tóxica conocida en seres humanos o animales. Los productos de NOMEX® no se derriten y, con un índice limitador del oxígeno (LOI) en 220°C sobre 20,8 (el valor crítico para la combustión en aire normal), no favorecen la combustión.
Aplicaciones del Kevlar y del Nomex
El Kevlar, en combinación con Nomex, es utilizado en una gran gama de productos hoy en día. Entre ellos, es utilizado para los chalecos y cascos antibalas, también en el desarrollo de cables ópticos, cordones para escalar, llantas, partes para aviones, canoas, raquetas de tenis y más.
Actualmente DuPont comercializa dos tipos de Kevlar:
El Kevlar 29, de baja densidad y alta resistencia, se utiliza principalmente para aplicaciones balísticas, cables y cuerdas.
El Kevlar 49, de baja densidad, alta resistencia y módulo elástico, se utiliza para reforzar plásticos de materiales compuestos para aplicaciones aeroespaciales, marina, automoción y otras aplicaciones industriales.
Como vemos las aplicaciones del Kevlar y el Nomex abarcan todos los campos sociotecnológicos:
Este chaleco de protección antibalas y antiimpactos está fabricado con una combinación de Kevlar y Nomex, donde el Nomex proporciona una resisencia adicional ante el fuego, las explosiones y la abrasión.
Protección para las fuerzas de seguridad:
Los policías necesitan ser equipados y entrenados para ocuparse de situaciones violentas y peligrosas, y esto significa tener la mejor ropa protectora personal posible. El chaleco se puede diseñar para balas, puñaladas, protección de impactos, o cualquier combinación de éstos. El equipamiento debe proporcionar también protección contra el fuego, el calor y el ataque químico. Estos elementos son fabricados en la actualidad a base de kevlar y nomex, los cuales nos garantizan estas propiedades además de ser cómodos y ligeros.
Un campo donde juegan un papel fundamental las ropas fabricadas a partir de Nomex y Kevlar es el de la equipación de los Tedax, desactivación de explosivos.
Protección para las fuerzas armadas:
El Kevlar se utiliza para muchos usos militares que se extienden en muchos ámbitos: la fragmentación y la protección antibalas, equipos antiminas, los bolsos de los paracaídas del asiento del eyector y los guantes protectores, entre otros. El Kevalar es hasta cinco veces más fuertes que el acero sobre una base del igual peso, por ejemplo, los cascos de Kevalr son más resistentes a los fragmentos de metralla que sus precursores de acero.
Los usos militares para el Kevlar incluyen el chaleco antibalas, toda la ropa del uniforme militar, cascos, guantes, cargadores, portadores de explosivos e incluso mantas balísticas.
Fuego y protección contra el calor:
El Nomex se utiliza para la fabricación de la ropa protectora antiincendios que se extienden desde los uniformes de la tripulación aérea hasta la ropa interior de los soldados.
La comodidad del Nomex, que puede ser tejido o ser hecho a punto incluso, se diseña específicamente para proporcionar transpiración. Además la ropa puede ser teñida en colores de camuflaje a la reflexión infrarroja.
Cada explosión causada por un misil, una bomba o una granada genera con frecuencia una bola de fuego. La munición y el combustible aceleran más dicho fuego particularmente en el interior de los aviones, vehículos de lucha armados y naves.
La ropa fabricada a apartir de fibras de nomex tiene una excepcional durabilidad, de hasta cinco veces mayor que el polyester/algodón usado para el mismo fin.
Aplicaciones eléctricas:
Dondequiera que haya una necesidad del aislamiento eléctrico, hay generalmente productos de Nomex para satisfacer dichas necesidades. En sus variadas formas, sobre todo los papeles y los cartones prensados, podemos usarlo para aislamiento en transformadores, motores eléctricos, los generadores y todo tipo de equipos eléctricos.
Protección térmica:
El Nomex se utiliza en todos los tipos de motoresde CA y CC, en servomotores, a 13.6kV y en generadores industriales vapor-turbina 150MW.
Los motores pueden alcanzar temperaturas considerablemente superiores a la de diseño debido a sobrecargas, humedad, desequilibrio de fases, en el arranque y la parada, etc.
Aplicaciones eléctrónica
El papel y el cartón prensado de Nomex se utiliza en equipos electrónicos por sus características ignífugas excepcionales. También ofrecen alta resistencia térmical y resistencia. Se utilizan generalmente en interruptores y controles, en dieléctricos, etc.
El Kevlar es una poliamida aromática denominada poli-(parafenileno tereftalamida), o PPTA, que se puede formular como:
Los anillos aromáticos confieren rigidez a las macromoléculas. En la figura 3a se indica como las macromoléculas de PPTA, que se encuentran unidas por enlaces por puentes de hidrógeno, forman hojas planas rígidas. Éstas se ordenan en forma de sistema radial de láminas plegadas axialmente (Figura 3b), constituyendo las fibras que presentan una marcada anisotropía [10].
Los procesos utilizados para fabricar estas fibras originan una orientación de las macromoléculas paralelamente al eje de la fibra, con la consiguiente mejora de las propiedades mecánicas en esa dirección. También, la estructura de las fibras es la responsable de la escasa resistencia a la compresión que exhiben estos materiales.
Las características destacadas, y comunes, a las diferentes fibras de Kevlar se pueden resumir en:
Alta relación resistencia mecánica/peso.
Rigidez estructural (elevado módulo de Young y bajo alargamiento a la rotura).
Elevada tenacidad. Resistencia a la fatiga.
Rotura dúctil, no frágil como las fibras de vidrio y de carbono.
Son aislantes eléctricos.
Alta resistencia química. Tolerancia general al deterioro ambiental, aunque la radiación ultravioleta puede degradar el material.
Pequeña contracción térmica.
Excelente estabilidad dimensional.
Alta resistencia al corte.
Elevado grado de estabilidad térmica (temperatura de descomposición, en aire: 425 ºC).
Baja conductividad térmica.

ARAMIDA
La primera fibra de aramida (para-aramida) surge, en los inicios de la década de los 70, como consecuencia de los trabajos de Stephanie Kwolek y colaboradores en DuPont [6]. Comercializada bajo el nombre de Kevlar, sus primeras aplicaciones fueron el refuerzo de neumáticos y de polímeros.
Las características de ligereza, alta resistencia mecánica y elevada tenacidad han permitido su utilización en numerosos sectores (materiales compuestos, sustitución del asbesto, fabricación de cables y tirantes para sujeción de diversos tipos de estructuras, protección antibalística, tejidos y ropas de protección personal...). Posteriormente, se han desarrollado otras fibras de aramida, entre las que destacan las resultantes de la mejora del primitivo Kevlar y las conocidas con las denominaciones comerciales de Twaron [7] y Technora [8].
Una clasificación útil de las fibras de aramida es la que se realiza atendiendo a los valores de módulos de elasticidad que presentan. De acuerdo con este criterio, resultan tres grupos de fibras:
De bajo módulo (“low modulus”, LM).
Con módulo intermedio (“intermediate modulus”, IM).
De alto módulo (“high modulus”, HM).
El módulo de Young específico es una propiedad clave para el empleo de materiales compuestos en la industria aeroespacial. Los valores de esta propiedad para las fibras de aramida son más elevados que los correspondientes a las fibras de vidrio, pero inferiores a los que se encuentran con las fibras de de carbono. La temperatura máxima recomendada para el uso continuado de estas fibras es de 160 ºC.

ACRILICO
Se define como fibra acrílica un polímero constituido por macromoléculas lineales cuya
cadena contiene un mínimo del 85% en masa de unidad estructural correspondiente al
acrilonitrilo.
El monómero de acrilonitrilo se descubrió en 1893 y el polímero se patentó por primera vez en 1929. El polímero puro era extremadamente insoluble hasta que se descubrió la dimetilformamida. Las fibras que están compuestas por un 10 % de acrilonitrilo tienen una estructura interna compacta, muy orientada, lo que hace virtualmente imposible el teñido. Por lo tanto la mayoría de las fibras acrílicas se fabrican como copolímeros, hasta 15% de aditivos que producen una estructura más abierta lo cual permite que los tintes sean absorbidos por la fibra. Los aditivos para el teñido son catiónicos para los tintes ácidos y aniónicos para los tintes básicos.
Hilatura de los filamentos de acrilonitrilo
La transformación de los copolímeros del acrilonitrilo en fibras, obliga a disolverlos y a extruir la disolución resultante en una atmósfera de aire o en un baño de coagulación.
El polímero se disuelve, para su hilatura, en un disolvente a base de dimetilformamida, en concentraciones, este último, del 15 al 40 % o más. Los sistemas actuales de hilatura son dos:
•Hilatura en seco.
•Hilatura en húmedo
Hilatura en seco
En la hilatura en seco los bloques de hilatura con las correspondientes bombas medidoras, equipo de filtración e hileras están situados en la cumbre o nivel superior de la cámara de hilatura. Inmediatamente debajo de cada hilera, una corriente de aire procedente de un jet circular incide sobre los filamentos en fase de formación.
En el interior de los tubos o cámaras de hilatura, cuya longitud es unos 6 m, la mayor proporción de disolvente es evaporado y arrastrado por la corriente de aire caliente.
En las proximidades de la base de la célula se recoge el aire saturado con vapor disolvente y se envía al equipo de condensación. El haz de filamentos es recogido en la base del tubo mediante una guía-hilos de cerámica.
Sobre este incide agua fría que al entrar en contacto con el cable de hilatura lo enfría y detiene la evaporación. Con este tratamiento acuoso se inicia también la eliminación del disolvente residual de los filamentos casi solidificados y las aguas de lavado se envían a la planta de recuperación del disolvente.
Después de abandonar la célula de hilatura se aplica un acabado a base de una emulsión de ensimaje, antes de que el haz de filamentos sea recogido por guías conducidas y enviado a un bote alimentador.
A causa de las altas temperaturas necesarias (230-260C°); para la evaporación del disolvente y la formación del filamento, la hilatura en seco obliga a adoptar precauciones especiales contra la explosión y penetración de vapores tóxicos en las áreas de trabajo.
Hilatura en húmedo
Los equipos de hilatura tipo balsa o piscina son actualmente los casi exclusivamente utilizados en la hilatura en húmedo. La solución de hilatura procedente de las bombas de hilatura y filtros individuales es extruida a través de las hileras, las cuales están distribuidas y sumergidas en el baño de coagulación por debajo del nivel del líquido.
La solución de hilatura contiene del 10 al 30 % de polímero y el baño de coagulación consiste en una disolución del disolvente de hilatura y su temperatura depende de la naturaleza o tipo de disolvente y oscila entre -5 y 45 C°.
A la salida del baño, los cables pasan por una serie de guías comunes después de ser acompañados por los rodillos guía medio sumergido.
Las variables más importantes de un proceso de hilatura en húmedo corresponden al disolvente y coagulante elegidos, y a las condiciones en que tiene lugar la coagulación. Para facilitar la recuperación del disolvente, el baño de coagulación suele consistir en una solución acuosa del mismo disolvente empleado para preparar él dope.
Entre los productos utilizados se pueden citar los siguientes: agua, alcoholes, soluciones acuosas salinas, kerosene, xilenos y glicoles.
La temperatura del baño de coagulación influye mucho en la calidad del producto obtenido. A este respecto, se ha observado que cuando la temperatura del baño se mantiene entre -15 y + 10 °C la extrusión del dope en una solución acuosa de tiocianato conduce a geles claros y tenaces, y que, después de convertidos en filamento, pueden ser estirados para aumentar la resistencia a la tracción y el trabajo de rotura del filamento. Cuando la temperatura es superior a + 1O °C los geles precipitados son opacos, poco tenaces y no se prestan a una posterior orientación.
El no cumplimiento de las condiciones óptimas de la coagulación puede ocasionar problemas y conducir a fibras con un aspecto áspero y poroso, a veces, de color blanco lechoso. El motivo puede ser una velocidad de coagulación demasiado alta o demasiado baja, ya que en ambos casos se dificulta la formación de una adecuada estructura de la fibra.
Propiedades generales
Dentro de la familia de las fibras acrílicas se presentan ciertas variaciones en las propiedades físicas y químicas. Estas diferencias pueden ser impuestas por las necesidades de unas aplicaciones específicas o debidas a diferencias en el proceso de fabricación de las diferentes productoras (sistemas de hilaturas) y a diferencias menores en su composición química. Por otra parte, las diferencias no son tan importantes como en otras fibras (poliéster, rayón) y ello permite establecer un intervalo de valores, mas o menos estrecho, en el que quedan incluidos todos los valores que para cualquier propiedad puede presentar cualquier fibra acrílica.
Se fabricaron fibras acrílicas de gran resistencia a la tracción (5,5 – 6,6 g/dtex), pero su comportamiento era muy deficiente por la facilidad con que fibrilaban, y por que la fibrilación ocasionaba un cambio de matiz en las zonas abradidas. Estos defectos se eliminaron disminuyendo la resistencia de los productos comerciales (vaporizado) y modificando ligeramente la estructura por copolimerización. La disminución de la tenacidad que se derivo de la incorporación de un segundo componente de la cadena polimérica no ocasiono ningún problema serio.
La tenacidad de las fibras acrílicas cumple satisfactoriamente con las necesidades o exigencias que imponen sus campos de aplicación. A este respecto, pronto se hizo evidente que su penetración en el mercado textil debía ser consecuencia más de su tacto agradable, resistencia, fácil cuidado y otras propiedades, que de su alta tenacidad.
Propiedades fisicas
•Aislamiento térmico
•Poder cubriente.
•Sensación seca.
•Resistencia a la abrasión y pilling.
•Mínima calibración de máquinas.
•Sentido del tacto.
•Resistencia a la luz solar.
•Fácilmente se carga de electricidad.
Aislamiento térmico, La mayor cantidad de bolsas de aire que se generan en el hilado, debido a la sección transversal en forma de hueso de la fibra, evita la perdida de calor en la prenda.
Poder cubriente, La forma transversal de esta fibra permite un mayor radio, superficie / volumen que las fibras que tienen secciones del tipo redondo, proporcionando una cobertura equivalente con menos fibra, obteniéndose prendas con menor peso.
Sensación seca. El espacio capilar entre fibras permite la eliminación de humedad, generándose así una agradable sensación de sequedad, que resulta particularmente ventajosa en confección de medias y calcetines.
Resistencia a la abrasión y pilling, las magnificas propiedades de tenacidad y resiliencia de esta fibra rinde una resistencia superior tanto a la abrasión como alpilling. Cuando la fibra es corta, sus muchos extremos que salen a la superficie de la tela se deterioran fácilmente con el roce, se enrollan entre sí y se aglomeran, frisándose, formando bolitas que dan mal aspecto e incluso me mezclan con otras fibras de otras telas. La resistencia de la fibra es inversamente proporcional al pilling.
Mínima calibración de máquinas, mediante un solo tipo de calibración, nos permite todos los tex o decitex del material, lo que evita el cambio de piñones.
Podemos regular la termoseccionadora con distintos estiros y temperaturas para lograr variedad de encogimiento de la fibra, obteniendo hilados con características distintas, lo que permite aumentar la cantidad de artículos.
Resistencia a la luz solar. Incluso expuestas al sol de forma permanente, son de gran aceptación para uso de exteriores, cortinas, visillos, banderas, etc.
Fácilmente se carga de electricidad. Esta característica suele hacer incomoda algunas prendas. Aprovechando otras buenas cualidades de estas fibras, se solventa el problema a base de mezclar fibras sintéticas con otras artificiales o naturales. En si misma es una cualidad muy a tener en cuenta cuando la fibra se utiliza en grandes superficies o en lugares donde una pequeña chispa, incluso eléctrica puede incendiarla.
Esta afinidad eléctrica propicia en ellas la adherencia de polvo y pelusas, problema que no se soluciona con el cepillado sin la previa descarga electrostática. En los procesos de confección, esta afinidad hace que las telas se adhieran a las máquinas, entorpeciendo su movilidad. Hay acabados de telas que reducen esta afinidad; pero el lavado continúo o la limpieza vuelva a cargarlas.
Propiedades quimicas
•Excelente resiliencia.
•Resistencia a polillas y microorganismos.
•Baja absorción de agua.
•Oleofílicas.
•Resistencia a la mayoría de agentes químicos.
•Fibras de alto encogimiento.
Excelente resiliencia, Se arrugan difícilmente; pero las deformaciones una vez producidas o fijadas son permanentes.
Resistencia a polillas y microorganismos. La primera consecuencia positiva de esta propiedad es que su almacenamiento no presentan los problemas que se dan con otras fibras o telas. El que estas fibras sean tan resistentes a los agentes orgánicos las ha llevado a una masiva utilización en ropa deportiva y de baño, artículos de viaje, tiendas de campaña y en el textil industrial no vestuario: bolsas, sacos, envolturas, artículos de pesca, etc.
Baja absorción de agua. Se limpian con facilidad las manchas de origen acuoso y secan con facilidad; son un tanto difíciles de teñir. Muy apropiadas para uso en el agua.
Oleofílicas. Su baja absorción del agua es paralela a su afinidad por los aceites y las grasas. Las manchas de este tipo deben eliminarse con productos de limpieza en seco.
Resistencia a la mayoría de agentes químicos. Propiedad que lleva a su uso a la confección de prendas apropiadas para el trabajo en laboratorios, cuando la fibra se colorea en el momento de su fabricación, después su color tiene excelente estabilidad.
Sensible a los ácidos y estable a los álcalis.
Fibras de alto encogimiento. Combinadas en el mismo hilo con fibras que no encogen, en un tratamiento con calor se consigue un hilo de gran volumen; si es sobre un tejido lo hace voluminoso.

POLIURETANOS
Se fabrica a partir de la reacción química de isocianatos y alcoholes polihídricos. En al año 1937 se fabricaban fibras de poliuretano competitivas con las poliamidas. Las principales aplicaciones de los poliuretanos han sido para aislamiento térmico, como las espumas, también los elastómeros, los adhesivos y recubrimientos superficiales. Los procesos de transformación son diferentes para cada caso. Los tipos lineales se pueden moldear por inyección, compresión o extrusión. Se pueden usar otras tecnologías como la hiladura en húmedo para hilados de calidad, o bien en los tipos reticulados, los sistemas normales de elaboración de la goma, pinturas y adhesivos. El poliuretano básico es formado mezclando dos líquidos, un alcohol polihídrico y un diisocianato. El entrecruzamiento es llevado a cabo con resinas epoxies con la adición de un tercer compuesto reactivo. Los poliuretanos tienen óptima elasticidad y flexibilidad, resistencia a la abrasión (5 a 6 veces más que el caucho) y al corte. Gran resistencia a los aceites minerales y grasas. Buena barrera al oxígeno, ozono y luz UV. Los usos más conocidos son: fuelles, tubos hidráulicos, paragolpes en la industria automotriz, juntas, empaquetaduras. Los más duros se emplean para piezas deslizantes, cápsulas, suelas para zapatillas, ruedas especiales.
Estructura Química
Los poliuretanos componen la familia más versátil de polímeros que existe. Pueden serelastómeros y pueden ser pinturas. Pueden ser fibras y pueden ser adhesivos. Aparecen en todas partes. El nombre asignado de poliuretanos viene de que su cadena principal contiene enlaces uretano.
Enlace Uretano
Propiedades principales
La mayoría de los poliuretanos son termoestables aunque existen algunos poliuretanos termoplásticos para algunas aplicaciones especiales.
Posee un coeficiente de transmisión de calor muy bajo, mejor que el de los aislantes tradicionales, lo cual permite usar espesores mucho menores en aislaciones equivalentes.
Mediante equipos apropiados se realiza su aplicación "in situ" lo cual permite una rápida ejecución de la obra consiguiéndose una capa de aislación continua, sin juntas ni puentes térmicos.
Su duración, debidamente protegida, es indefinida.
Tiene una excelente adherencia a los materiales normalmente usados en la construcción sin necesidad de adherentes de ninguna especie.
Tiene una alta resistencia a la absorción de agua.
Muy buena estabilidad dimensional entre rangos de temperatura desde -200 ºC a 100 ºC.
Refuerza y protege a la superficie aislada.
Dificulta el crecimiento de hongos y bacterias.
Tiene muy buena resistencia al ataque de ácidos, álcalis, agua dulce y salada, hidrocarburos, etc.
Propiedades mecánicas
Las propiedades mecánicas dependen de la medida de su peso volumétrico; a medida que este aumenta, aumenta su propiedad de resistencia. Los pesos volumétricos más usuales se hallan comprendidos entre 30 y 100 kg/m3, dentro de estos límites se obtienen los siguientes valores:
- Resistencia a la tracción entre 3 y 10 (Kp./cm2)
- Resistencia a la compresión entre 1,5 y 9 (Kp./cm2)
- Resistencia al cizallamiento entre 1 y 5 (Kp./cm2)
- Módulo de elasticidad entre 40 y 200 (Kp./cm2)
Resistencia a los productos químicos
El poliuretano es resistente al agua potable, al agua de lluvia y al agua de mar, las soluciones alcalinas diluidas, los ácidos diluidos, los hidrocarburos alifáticos como por ejemplo la gasolina normal, el carburante diesel, el propano, el aceite mineral, así como los gases de escape y el aire industrial (SO2). Es condicionalmente resistente (hinchamiento o encogimiento) a los siguientes productos: los hidrocarburos clorados, las acetonas y los éteres, no es resistente a los ácidos concentrados.
Comportamiento ignífugo
En el sector de la construcción se emplean exclusivamente materias primas que dan lugar a una espuma sintética autoextinguible. Mediante la combinación de una capa cubriente incombustible se alcanza el predicado (difícilmente inflamable), según DIN 4102.
Poder adhesivo
Una propiedad particularmente interesante del poliuretano es para el empleo como material de construcción por su adhesión a diferentes materiales. Durante la fabricación la mezcla experimenta su estado intermedio pegajoso y en virtud de la fuerza adhesiva propia, automática y excelentemente se adhiere al papel, al cartón y al cartón asfaltado para techos, así como a las maderas, a las planchas de fibras duras y de virutas prensadas, a la piedra, al hormigón, al fibrocemento, a las superficies metálicas y a un gran número de materias plásticas.
Los poliuretanos tienen en general las siguientes características:
excelente tenacidad.
flexibilidad, alta capacidad de alargamiento.
excelente relleno de holgura.
puede pintarse una vez curado.
excelente resistencia química.
Aplicaciones
Material de construcción
Los poliuretanos son una solución a la necesidad de materiales especiales en construcción. Los productos de poliuretano y las correspondientes tecnologías permiten una fabricación económica.
Los sistemas de construcción progresan y las necesidades de conservar la energía aumentan, la espuma rígida de poliuretano puede ser el producto óptimo para llegar a estos objetivos. Proporcionan el aislamiento más eficiente a disposición de la industria de la construcción y refrigeración. El poliuretano se combina fácilmente con los materiales de acabado superficial disponibles, ofreciendo la posibilidad de producir diferentes compuestos. Desde cámaras frigoríficas hasta generadores de energía (donde se debe eliminar cualquier posibilidad de condensación de agua en el techo), son algunos ejemplos. En la técnica de la calefacción y refrigeración los poliuretanos se usan para aislar tuberías, para el caso de tener que aislar grandes superficies se utiliza el método de aplicación por aspersión. La espuma rígida puede ser obtenida en forma de placas aislantes para techos y paredes o se puede inyectar para llenar cavidades. Ahí donde se requiera un aislamiento de baja conductividad, alta resistencia y bajo peso, se puede usar una espuma rígida de poliuretano.
A diferencia de la espuma rígida, la espuma flexible de poliuretano posee una estructura celular abierta, es un material muy elástico, que cuando se retira la carga a la que haya sido sometida, recupera instantáneamente su forma original. Es un material sumamente ligero y con una alta permeabilidad al aire, escogiendo las materias primas en su fabricación y variando la formulación, podemos regular sus propiedades: la amortiguación, la característica elástica, la estructura celular, la densidad aparente y la dureza.
Campos de aplicación importantes se encuentran en las industrias fabricantes de asientos para coche, sillas y colchones, también se aplican para embalar equipos delicados, en artículos para hospitales, etc.
Adhesivos
Los poliuretanos se forman por un mecanismo en el que el agua reacciona (en la mayoría de los casos) con un aditivo formulado que contiene grupos isocianato. Al igual que en el caso de las siliconas, la molécula de agua ha de migrar al interior del adhesivo, donde se produce el enlace. Su comportamiento de curado es por ello el mismo que el de las siliconas, pero sin liberar subproductos al medio ambiente. La velocidad de curado también depende de la humedad relativa, al igual que en el caso de la silicona.
Para conseguir la mejor y más duradera adhesión se recomienda el uso de productos apropiados de limpieza e imprimación (promotores de la adhesión). Se utilizan diferentes imprimaciones en función de los sustratos.
La aplicación de espuma de poliuretano mediante spray no sólo brinda una excelente aislación térmica y anticondensante, sino también una perfecta impermeabilización. Esto se debe a que el 90% de las celdas son cerradas y actúan como una barrera continúa a la penetración del agua. Mientras que en las cubiertas planas convencionales es preciso instalar por superposición gran número de capas, con diversas funciones para cada una, en los recubrimientos por proyección se utiliza, en principio, solo un material, que por su resistencia mecánica y su adherencia sobre toda la superficie, mejora la rigidez estructural de todo tipo de estructura.
Este sistema tiene especial importancia para el saneamiento y la renovación de la protección termohidrófuga de techados deteriorados, como así también para edificaciones nuevas de hormigón o chapa.
Lacas, pinturas y esmaltes
Pintura impermeabilizante para techos
Las lacas y pinturas de poliuretano se han convertido en una garantía de durabilidad, resistencia y belleza ampliamente aceptadas hoy.
Los poliuretanos son una amplia variedad de polímeros con diferencia total en su composición y sus correspondientes propiedades. La multitud de estructuras y la posibilidad de diseñar polimeraciones está ligada a la necesidad que exija el fabricante de muebles o piezas en madera. Así, un mueble que tenga como protección pinturas de poliuretano garantiza su resistencia al calor, al rayado, a sustancias químicas y al manchado de agua, ya que revisten la pieza con una película de tal dureza, que en condiciones naturales puede mantener su estado original durante diez años sin ninguna alteración; que no es el caso de los otros productos que garantizan solo la mitad del tiempo.
En la actualidad, aproximadamente el 95 por ciento de la industria nacional del mueble da sus acabados con catalizadas y la razón es su costo, son mucho más económicas que las de poliuretano. La causa de la diferencia de precios obedece a que las resinas que componen los productos de poliuretano son muy caras y encarecen considerablemente los productos. De aquí, que son pocas las empresas que fabrican muebles con acabados en poliuretano todavía aunque es una empresa en auge.
No hay duda que las ventajas que ofrece el poliuretano superan ampliamente a otras del mercado que ofrecen un servicio similar. De hecho, las ventajas en resistencia a la abrasión y al rayado le permiten ser usado en pisos muy transitados sin que se deteriore por tráfico continuo. En la actualidad, el poliuretano se aplica con éxito en otros materiales como el metal. Los aviones, equipos, maquinaria y estructuras son recubiertos con esta película para protegerlos de los cambios bruscos de temperatura, aprovechando que su proceso de catálisis es por reacción química y no por contacto con el aire. En este momento la línea poliuretano ofrece una amplia gama de productos de acuerdo a la necesidad. Cada uno tiene una composición que puede mezclar hasta tres componentes y brindar distintos grados de dureza, brillo, resistencia a temperaturas e intemperie, agentes químicos y otros.
Tipos:
Lacas uretánicas de dos componentes para madera uso interior y exterior. Se componen de poliol elaborado a partir de resinas hidroxiladas que pueden ser acrílicas, poliestéricas libres de aceites y modificaciones, y endurecedor, elaborados a partir de TDI, MDI, IPDI y un glicol.
Barniz mono componente para pisos de madera. De excelente dureza y flexibilidad, elaboradas a partir de TDI - glicol. El secado de este se produce por reacción con la humedad ambiente la cual actúa como su catalizador.
Barniz alquídico - uretánico. Se elabora a partir de resinas alquídicas uretanizadas con TDI - IPDI y aceites tales como linaza y soya. Su manejo es muy generalizado en Europa y Estados Unidos para usos domésticos. Su resistencia es mucho menor a las anteriores e igualmente su costo, pero supera en cualidades físicas y químicas de secado a los esmaltes y barnices alquídicos disponibles en el mercado suramericano.
Laca Exterior.
· Tipo: Laca grado uretano, de un componente. Se recomienda para maderas expuestas a la intemperie como cabañas, puertas, ventanas.
Propiedades y características: Excelente brillo, resistente al rayado, detergentes, abrasión, intemperie y solventes. Protege y embellece.
Laca Intemperie.
Tipo: Laca en poliuretano de acabado. Todo tipo de madera. Puede utilizarse en exteriores e interiores. Protege objetos o accesorios de madera. Propiedades y características: Gran dureza y resistencia mecánica y química. Posee alto brillo, dejando superficies tersas con sólo dos o tres capas de pintura.
Laca Pisos
Tipo: Laca de poliuretano para máxima protección de pisos de madera en interiores.
Propiedades y características: Protege contra la abrasión, solventes, soluciones ácidas, soda cáustica, productos químicos con un excelente brillo. No necesita encerar ni se craquela.
Aplicaciones de los TPU (poliuretanos termoplásticos)
Los poliuretanos termoplásticos (TPU) poseen una estructura que les proporciona unas propiedades que otros tipos de polímeros no poseen y que los hacen muy útiles para aplicaciones de altas prestaciones:
Excelente resistencia a la abrasión.
Excelentes propiedades mecánicas, combinadas con gran elasticidad.
Gran resistencia al desgarre.
Muy buena resistencia a aceites y grasas.
Muy buena elasticidad a bajas temperaturas.
Tradicionalmente los TPU se clasifican en dos grandes grupos en función de su naturaleza:
-TPU basado en poliéter (generalmente politetrahidrofurano).
-TPU basado en poliéster (generalmente derivado del ácido adípico).
El TPU basado en poliéter posee mejor resistencia a la hidrólisis, mejor resistencia a los microorganismos y mejor flexibilidad a bajas temperaturas. Por su parte, el TPU basado en poliéster presenta mejor resistencia a la termooxidación y mejor resistencia a los aceites y grasas.
Hay un nuevo TPU base poliéter para aplicaciones donde es necesaria una gran resistencia a la hidrólisis y TPU de diferente dureza basado en copolímero de poliéter que reúnen las mejores prestaciones de los TPU basado en poliéter y en poliéster: buena resistencia a la hidrólisis combinado con una buena resistencia a la termooxidación y excelentes propiedades mecánicas.
Nuevas tendencias y desarrollos:
Las mejores perspectivas para los TPU están centradas en el área entre el caucho convencional y los termoplásticos rígidos. Las aplicaciones tecnológicas y los nuevos diseños se esfuerzan para sacar provecho de sus propiedades únicas para crear productos innovadores a precios razonables.
- TPU más blandos:
Por debajo de una dureza de 80 Shore A, los TPUs tienden a largos tiempos de ciclo de inyección y, consecuentemente, la producción es menos rentable. Estos productos se pueden obtener por la adición de plastificantes a TPUs más duros pero siempre es un compromiso por los problemas que dicho aditivo comporta (exudación y pérdida de propiedades mecánicas). Un mercado potencialmente interesante es el de TPUs blandos sin plastificantes para artículos que precisan altas propiedades mecánicas y buena resistencia a disolventes.
- TPU con alta resistencia a la temperatura:
Los desarrollos en este campo son interesantes en dos sectores de aplicación: Films.
El mercado requiere productos que, una vez procesados, posean un alto punto de fusión por estar en contacto continuado con zonas calientes. Es el caso de films de poliuretano utilizados en la industria del automóvil (para insonorización de motor).
- TPU altamente estables a la luz:
El amarilleo por exposición a la luz es un gran inconveniente en algunas aplicaciones. La utilización de combinaciones efectivas de absorbentes UV y el uso de isocianatos alifáticos permiten obtener TPUs con alta estabilidad a la luz. Estos productos presentan peores propiedades mecánicas y son más caros, pero son también buenos candidatos para aplicaciones biomédicas por su baja toxicidad. El reto está en obtener productos de alta calidad, con muy buena estabilidad a la luz y a precios competitivos.
- TPU como alternativa al PVC plastificado. "Slush moulding":
Se trata de formulaciones especiales de TPU en polvo aplicadas por sinterización rotacional en la industria del automóvil. Se utiliza para recubrir partes interiores del automóvil que precisan tacto imitación a piel.
Fases del proceso:
Colocación del polvo en el molde previamente calentado.
Aplicación de vacío y rotación o vibración del molde para repartir el polvo uniformemente por su superficie caliente donde funde y la cubre en forma de piel.
Enfriado del molde.
Traspaso de la "piel" a la superficie de la pieza a recubrir (a menudo espuma de polietileno).
El producto aplicado por este sistema debe tener unos requisitos básicos:
Fusión homogénea.
Viscosidad del fundido adecuada.
Granulometría muy fina (50-500μm).
Fácil desmoldeo.
Alta resistencia a la luz.
Color estable.
El TPU, además, posee muy buena adhesión a la espuma de polietileno, se comporta mejor a temperaturas extremas y es más agradable al tacto que otros polímeros utilizados en esta aplicación.
El deporte y los poliuretanos termoplásticos
Muchísimos fabricantes de artículos deportivos utilizan hoy en día los poliuretanos. Debido a su resistencia y duración, son ideales para las cámaras de aire que se utilizan en balones, cascos de ciclistas, y en productos laminados sobre tejido como los compensadores de lastrado para submarinistas, e incluso como capas antirasguños de las que se colocan en el fondo de las embarcaciones inflables. La resistencia a la tensión y a la abrasión de estos poliuretanos y su facilidad de fabricación explican su duradero rendimiento.
Las cámaras de aire que se usan en balones, cascos, calzados y otros equipos tienen que ser sólidas por mucho tiempo y mantenerse intactas contra "malos tratos" de todo tipo como golpes, presiones, estrujamientos y flexiones. Además de estos "malos tratos", tienen que resistir las inclemencias naturales, incluyendo las temperaturas extremas y la humedad. Los poliuretanos termoplásticos dan a estas cámaras de aire la necesaria resistencia a la tracción y al reventamiento, junto con la elasticidad y la flexibilidad que hacen falta para aguantar los golpes. Tienen una excelente resistencia a la fatiga por flexión y conservan sus propiedades en toda clase de condiciones excesivas, incluyendo calor y frío extremos. Y como no contienen plastificantes, conservan sus propiedades durante una larga vida útil.
Otra ventaja es su facilidad de fabricación. Es un material con el que se trabaja fácilmente, lo que simplifica la producción y reduce los costos. Puede fabricarse de muchas maneras: en sacabocados, o bien sellado a altas frecuencias, termopegado, formado en vacío, laminado en caliente o bien como adhesivo pegado con otros poliuretanos u otras materias. Puede estamparse o serigrafiarse. Las cámaras de aire de poliuretanos termoplásticos se suelen usar en balones de fútbol, de voleibol o de rugby y para conformar los cascos de ciclismo, los patines de hockey y el calzado de atletismo. Las cámaras de gel se usan para plantillas ortopédicas o antichoques en el calzado.
Otras aplicaciones deportivas, en las cuales se los utilizan, son las compresas de agua fría aplicadas a las heridas que sufren los atletas en las articulaciones. Este tipo de productos no sólo se beneficia de las cámaras de TPU para contener y hacer circular los fluidos en cuestión sino que utiliza poliuretanos termoplásticos laminados sobre tejido para proteger las heridas con un envoltorio que no pierde flexibilidad a temperaturas muy bajas.
Laminados La resistencia y durabilidad del TPU lo convierte en un excelente material para laminarlo sobre diversos tipos de tejidos, combinación que se utiliza en una gran variedad de artículos deportivos. En función de las necesidades, se aplica una capa muy fina que proporciona resistencia a la tensión y a la abrasión así como impermeabilidad. Además, sirve de adhesivo versátil para pegar juntos varios materiales.
Los laminados para compensadores de lastrado en el deporte submarino utilizan los poliuretanos por su resistencia a la abrasión y a la fatiga causada por la flexiones. Por otro lado, los laminados de TPU facilitan el diseño de sistemas impermeables, lo que es esencial para equipos submarinos y otras aplicaciones. Pueden ser sellados dieléctricamente en vez de tener que coserse, lo que explica que se trate de productos sin suturas (que tienen que ser obturados luego con un revestimiento impermeable). Además, hay artículos de protección como, por ejemplo, almohadillas de cascos de rugby, que usan poliuretanos termoplásticos como adhesivo entre una capa de tejido y la espuma aislante para una mejor protección exterior. Se usan también estos laminados para pegatinas, calcomanías o parches con números o nombres que se imprimen en un tejido con una plancha.
Los laminados de TPU se suelen usar también en material de camping. Son impermeables pero dejan pasar el aire y dan protección, durabilidad e impermeabilidad a los tejidos de las tiendas de campaña y de mochilas y prendas para la lluvia. Hay colchones inflables de camping que llevan una capa antigolpes de espuma pegada al tejido o al nylon con TPU. Los poliuretanos termoplásticos proporcionan a esos colchones resistencia y durabilidad para mantener inseparables sus distintas capas y evitar los agujeros por los que se escapa el aire.
Versatilidad y posibilidades de diseño
Los poliuretanos termoplásticos son un material sumamente polifacético que ofrece una amplia gama de opciones de diseño. Su facilidad de fabricación, su durabilidad, su resistencia a la tensión y a la flexión y demás propiedades de alto rendimiento explican que sean ideales para las duras exigencias del deporte y de los productos de recreación.
Los poliuretanos son perfectos para situaciones rigurosas y usos exigentes en que el material no puede ni debe fallar. Se pueden fabricar en películas o láminas en espesores desde 0,025 mm a 3,2 mm y a anchuras de hasta 203 cm. Este material está disponible con durezas de 75 a 95 Shore A, en muy diversos colores y en varios grados de opacidad y de texturas de superficie.
Inconvenientes
El inconveniente principal que tienen las espumas de poliuretano, es que son degradadas por los rayos ultravioletas, por lo cual no pueden quedar expuestas a la radiación solar, debiendo ser protegidas de los mismos en el caso de aplicaciones exteriores. También hay que tener en cuenta que para que se produzca la reacción deseada es necesario que el sustrato a aplicar tenga una temperatura mínima de 10ºC.
Reciclaje
Otro gran inconveniente que presenta los poliuretanos en general, es que son difíciles de reciclar o el proceso es poco rentable.
Reciclaje mecánico
Los poliuretanos pueden ser triturados y una vez están convertidos en polvo pueden reutilizarse en la producción de nuevas espumas.
- Los gránulos de espuma flexible finamente triturados pueden ser enlazados entre ellos dando lugar a una variedad de productos que se usan en las prendas deportivas. Estos productos enlazados se pueden enlazar otra vez dando lugar a un ciclo de aprovechamiento que puede llegar a ser bastante largo.
- Sometidos a elevada presión los gránulos de poliuretano se envuelven con un material que se adhiere a ellos, si en ese momento se curan en condiciones de calor y presión óptimas se puede obtener un material aprovechable como por ejemplo el piso del habitáculo de un coche.
- Si se modelan por compresión se producen espumas rígidas de poliuretano de los gránulos triturados, dando lugar a un material tridimensional que se usa para alojar el motor de los coches.
Recuperación energética
Se están estudiando nuevas tecnologías para convertir los poliuretanos de desecho en energía utilizable. En algunos experimentos propuestos por la PURRC (Polyurethanes Recycle and Recovery Council, USA) se aumentó la cantidad de desperdicios quemados por una planta incineradora en un 20% en peso con poliuretanos, encontrando que las emisiones de ceniza no habían aumentado significativamente. En Europa la ISOPA (European Isocyanate Producer Association) controla la incineración de poliuretanos, la energia que se desprende de este proceso se usa en producir energía eléctrica.
Reciclaje químico
Este reciclaje ha sido el resultado de unos 200 procesos de patentes, dando lugar a los métodos siguientes.
- La glicólisis es un proceso por el cual los poliuretanos reaccionan con dioles a una T alrededor de 200 °C produciendo polioles, un producto interesante en la producción del poliuretano en bruto.
- La hidrólisis puede producir tanto polioles como aminas intermedias para los procesos de síntesis de poliuretanos. Una vez recuperados los polioles también pueden ser usados como combustible.
- La pirólisis es un proceso que transforma los poliuretanos y los plásticos en gas y gasoil en condiciones de calor sin oxígeno.
La pureza de los gases y aceites derivados de los procesos de pirólisis e hidrogenación y el costo de producir los productos finales son asuntos importantes que hace falta resolver.

POLIVINILICOS
Alcohol de polivinilo El alcohol de polivinilo (PVOH, PVA, o PVal), también llamado polietenol o poli (alcohol vinílico), es un polímero sintético soluble en agua, de fórmula química general (C2H4O)n. No debe confundirse con acetato de polivinilo, un popular pegamento de madera.
Estructura química y síntesis
La estructura química abreviada del alcohol de polivinilo es la siguiente:
Propiedades El alcohol polivinílico tiene excelentes propiedades para formar películas, como emulsionante y como adhesivo. También es resistente al aceite, grasas y disolventes. Es inodoro y no tóxico. Tiene alta resistencia y flexibilidad, así como alta propiedades de barrera para el oxígeno y los aroma. Sin embargo, estas propiedades dependen de la humedad, es decir, con mayor humedad más agua es absorbida. El agua, que actúa como un plastificante, a su vez reducirá su resistencia a la tracción, pero aumentan su elongación y resistencia al desgarro.
El PVOH es totalmente degradable y se disuelve rápidamente. El PVOH tiene un punto de fusión de 230°C y 180-190ºC para los grados totalmente hidrolizado y parcialmente hidrolizado respectivamente. Se descompone rápidamente por encima de 200°C.
El poli (alcohol de vinilo) no funde como un termoplástico, sino que se descompone por pérdida de agua de dos grupos hidroxilos adyacentes a temperaturas superiores a 150°C. Los enlaces dobles permanecen en la cadena y, a medida que se forman más en posiciones conjugadas, tiene lugar una coloración importante.
Aunque el poli (alcohol de vinilo) es amorfo cuando no está estirado, puede estirarse dando una fibra cristalina por ser los grupos hidroxilo lo bastante pequeños para encajar en un retículo cristalino a pesar de la estructura de cadena atáctica.
El poli (alcohol de vinilo) es soluble en agua. Se disuelve lentamente en agua fría, pero lo hace más rápidamente a temperaturas elevadas, y puede normalmente disolverse a más de 90°C. Las disoluciones acuosas no son particularmente estables, especialmente si hay presentes trazas de ácido o base. Las disoluciones pueden sufrir una compleja serie de reacciones de gelación reversibles e irreversibles. Por ejemplo, puede producirse entre-cruzamiento en los enlaces éter, lo que resulta en un aumento de viscosidad por la formación de productos insolubles.
EI poli (alcohol de vinilo) puede reacetilarse por calentamiento con un exceso de anhídrido acético en presencia de piridina. El poli (acetato de vinilo) resultante puede o no tener la misma estructura que el polímero madre a partir del cual se obtuvo el alcohol, debido a la naturaleza de la estructura de cadena ramificada del polímero.
Usos El alcohol polivinílico es la materia prima para hacer otros polímeros como: - Nitrato de polivinilo (PVN): Se trata de un éster del ácido nítrico y el alcohol de polivinilo. El nitrato de vinilo se puede utilizar en algunos propulsores y explosivos moldeables. - Polivinil acetales: los poli(acetales de vinilo) se preparan por reacción de aldehídos con el alcohol de polivinilo. El polivinil butiral (PVB) y polivinil formal (PVF) son ejemplos de esta familia de polímeros. Se preparan a partir de alcohol de polivinilo, por reacción con butiraldehído y el formaldehído, respectivamente. La preparación de butiral de polivinilo es el mayor uso del alcohol polivinílico en los EE.UU. y Europa Occidental.
El polímero más importante, por mucho, de entre ellos es el poli (vinil butiral), que se usa como capa plástica intermedia para los vidrios de seguridad de aviones y automóviles. El poli (vinil formal) se utiliza en esmaltes para recubrimientos de cables eléctricos y en tanques de gasolina de auto-sellado. El alcohol polivinílico se utiliza como ayuda en la polimerización en emulsión, como coloide protector, para hacer dispersiones de acetato de polivinilo. Esta es la aplicación más grande del mercado en China.
En Japón, su uso principal es la producción de fibra vinylon o vinalon. En las fibras de poli (alcohol de vinilo), la forma final del polímero es insoluble en agua como resultado de un tratamiento químico. El polímero se hila en húmedo a partir de agua caliente pasando por una disolución acuosa concentrada de sulfato de sodio que contiene ácido sulfúrico y formaldehído. El polímero se insolubiliza por la formación de grupos formal:
Las fibras de poli (alcohol de vinilo) poseen una absorción de agua (un 30 %) superior a las demás fibras. Pudiendo de este modo reemplazar al algodón en aquellos usos en los que la fibra está en contacto con el cuerpo. El tacto del tejido puede variarse de similar a la lana a similar al lino. Esta fibra se lava fácilmente, se seca pronto y tiene buena estabilidad dimensional. La tenacidad y resistencia a la abrasión son buenas.

Comments